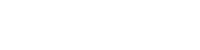
Steven Weagel of Pequot Lakes Blows Glass
Season 13 Episode 13 | 27m 13sVideo has Closed Captions
The glass & metal art of Steven Weagel of Pequot Lakes, MN
Crossing Arts Alliance in Brainerd, MN exhibits the glass & metal art of Steven Weagel of Pequot Lakes, MN. Lisa Ackerman (Jordan) prepares the Crossing Arts Alliance gallery as Steven demonstrates his glass blowing process at the state-of-the-art facilities of Vandalia Glassworks, in South Saint Paul, MN, making a colorful lamp shade.
Common Ground is a local public television program presented by Lakeland PBS
This program is made possible by the Minnesota Legacy Amendment and members of Lakeland PBS.
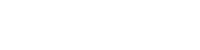
Steven Weagel of Pequot Lakes Blows Glass
Season 13 Episode 13 | 27m 13sVideo has Closed Captions
Crossing Arts Alliance in Brainerd, MN exhibits the glass & metal art of Steven Weagel of Pequot Lakes, MN. Lisa Ackerman (Jordan) prepares the Crossing Arts Alliance gallery as Steven demonstrates his glass blowing process at the state-of-the-art facilities of Vandalia Glassworks, in South Saint Paul, MN, making a colorful lamp shade.
How to Watch Common Ground
Common Ground is available to stream on pbs.org and the free PBS App, available on iPhone, Apple TV, Android TV, Android smartphones, Amazon Fire TV, Amazon Fire Tablet, Roku, Samsung Smart TV, and Vizio.
Providing Support for PBS.org
Learn Moreabout PBS online sponsorshipLakeland PBS presents Common Ground, brought to you by the Minnesota Arts and Cultural Heritage Fund and the citizens of Minnesota.
Production funding of Common Ground is made possible, in part, by First National Bank Bemidji, continuing their 2nd century of service to the community.
Member FDIC.
instrumental music....
Welcome to Common Ground.
I'm Producer/Director Scott Knudson.
In this episode, Steven Weagel, of the Pequot Lakes area, displays his artwork at the Crossing Arts Alliance in Brainerd, Minnesota, and demonstrates his glass blowing at Vandalia Glassworks in South St. Paul.
Hello, my name is steven Weagel.
I'm from Pequot Lakes, Minnesota, and I'm a glass and metal artist.
We're here at the Crossing Arts Alliance in Brainerd, Minnesota at an exhibition called "Light, Color, and Minnesota Landscape.
I've created the shades down at Vandalia Glassworks in South St. Paul, and I've done all of my metal work.
I'll start this at my studio outside of Pequot Lakes.
Before I start adding color to a piece, I want to create a form.
Harvey Littleton wrote a book way back and the name of his book was "A Search for Form" and for most of us glassblowers , as we learn to create glass and we learn to control the glass and we learn to create new shapes, then, the main concern for me is that it's got a good form, and form, it's called "form sense" by other artists, and form sense only comes from a lot of trial and error and a lot of work.
My first thought is, "what form do I want,", "is this going to be a good form," and "how do I get there."
Once I have the forms worked out in my head and in the glass, then I can begin to add color to it and let the color enhance the form.
I'm going to reheat it.
For most of us, as glass blowers, we're always in a search for form.
Of course, that's endless, that's infinite, the old medieval guild symbol for glass workers was a female symbol with infinity on top of it.
That is what glass is, glass is infinite .
Let's go to Vandalia Glassworks in South St. Paul, Minnesota.
This is a unique situation.
This is one of the finest studios in the country.
Essentially, I will be going here, opening this door, and gathering.
Then I will come out of there, and generally, I will go to the bench, and I will use this tool called a block, okay, and then I will be here.
I will be in and out of here constantly, and then back to the bench.
So, that's where I get, there's about 300 pounds of molten glass in there, that's the melter, or the furnace.
Back in the old days, we did everything with gas, and it was a kind of a standing joke that an "electric furnace", because it's cost prohibitive.
Well , now the price of propane and natural gas has gone up to the point that electricity is a viable solution, and the nice thing about electricity is, you can seal that tight.
With propane or gas, you've got to relieve the pressure.
With electric, you can have it shut tight and hold all the heat in there.
This is relatively new in the last 10-15 years.
When I started blowing glass in 1968-1969, we had to build everything, and now there's a whole industry that build these commercial units.
This is totally state of the art.
Craig, over here, has been blowing glass for 40 years also, and we both feel the same way, we walk in here and it's like we're kids in heaven.
There's a lab here.
"Hardest working glassblower in Minnesota right here, this guy right here.
Okay.
So, take a smaller gather, you can just see the glass; actually, it reflects like water so as I approach the glass with my blowpipe, I'm looking for the reflection, and as soon as I see the my blowpipe in the reflection, I know I'm close, because I don't want to have it too deep.
I don't want to have glass way down on the blowpipe.
We'll let that chill just a little bit.
i don't like too much glass up on the pipe, it's a waste of glass, and it causes other problems, so I take two small gathers to start, instead of trying to do it all in one gather.
I just set that up so there's enough glass on there to have a foundation for a shade.
This time I'm going to start with white, because I want a base behind the color, and because it's going to be lit from the inside.
I want it to be somewhat opaque, I want the light to diffuse when I turn it on, and so what happens is, I get dichroic glass.
I get glass that's one color when the light is reflected off of it, and when the light is turned on, it's now transmitting light and it changes color.
I'm going to put another layer of white and then I'm going to get that melted back in.
Now, I'm just building up the color, so you can see it's kind of lumpy, I want that to get nice and smooth and I will build up layer upon layer.
Okay, I'm coming out, and I'm going to begin to build up the blue, so that's called aquamarine, and this blue is fairly opaque.
I'm going to stick with a fairly light blue, and then I'm going to put dark blue designs into it.
Okay, you're good.
Now I'm going to do one layer of a deep cobalt blue, and you can see this is really fine.
Now you can see how much that changed.
Now, what I'm going to do is heat in again, and I'm going to go back to that lighter blue, and that will give me variations, with the dark blue peeking out from behind the lighter blue.
The aquamarine, this color is.
This doesn't take as long to fuse in, because it's so fine.
Okay, we'll do now, we'll go back one more in the aquamarine.
i'm just going to block this, just to get it off the pipe a little bit.
Now what I'm going to do is, I'm going to get it into that optic mold.
Nice and hot, okay, see the ridges?
I'm going to give this a quick heat and I'm going to go over there to the color, see how I'm twisting that, now look at the color, how it's gone into those low spots.
I'm gonna do that one more time, I'm just gonna heat this enough to fuse it, and I'm gonna pick up just a little more.
Now, I'm going to get it really hot again and then I'm going back to that optic mold.
Now, as I go in here, I'm going to have lines go across the lines that are there.
Quick reheat, and then I'm going back to that fine powder again, only this time I'm going to turn it in the opposite direction, so I will twist it across the lines that were there.
I've got the color set up, we'll fuse everything, I'll get it really really hot, I'll block it, and I'll blow a bubble into it.
So, occasionally, I'll just come out ..and like now, can you see the pattern that formed in there?
It's very subtle right now, but as I blow it out, it will become much more apparent.
I've got to get this really hot so I've got to be a little patient here.
I take my block again.
I'm gonna go reheat once more, it's not doing quite what I would like it to.
Okay, that's better, now I'll block it again, okay, then I'm gonna blow.
I've gotta add a little heat.
All right, we'll let that settle back a little bit.
All right, it just started to blow, I stop immediately, and I will block that.
Now we're starting to get some really nice interesting things happening with that color.
I don't want to blow that out too much, so I just barely puffed that one.
Okay, we've got the bubble set up, I've got the white peeking through, I've got the light blue peeking through, and the dark blue is on the outside.
I'm going to let this cool.
Now, these tools we use are made out of fruitwood; in this case, these happen to be applewood that I've saved.
Cherrywood works, and the reason we use fruitwood is it's really hard on an end cut, and it doesn't have any resins that mark the glass, but most importantly, we use we use cherrywood or applewood, the fruitwoods, because they don't rot in water.
So, most of these tools have been in water for 3 - 4 years before I ever carved the wood.
I store the wood in big tubs, and as I need it, I take it out and carve it, form it, whatever it is I need to make.
Most people think it's because it doesn't mark, but one of the main reasons is - it'll last forever in water.
It'll last longer in water than drought, than being out in the air.
Okay, we're ready for a big gathering You can make a nice big shade with that amount.
Could have taken a little less, but I can make this work.
You can see how easily that could have gotten away from me.
Once it laps up on that block like that, if a person isn't paying attention, it can lap up onto an arm or a hand, but that's not going to happen, we've got it under control.
I'm going to put a neckline in it while it's still good and hot.
There are other ways to do this, but I'm kind of "old school" and this is the way I like to work the glass.
Some people use wet paper to do this part.
All right, I've got that nice and centered, I'll block it one more time.
I'm going to go reheat and then I'm going to neck it again and probably reheat one more time.
Then, I'm going back over to there, over there to those optic molds.
I still need to keep that bottom, heavy.
Okay, back to reheat.
Now, we'll start forming the shape, make sure I've got a good neckline, till the bottom, blow it out, till the bottom, blow it out, and again, I have to make certain I keep that bottom tilled or it'll get paper thin.
Okay, I'm going to reheat again.
Okay.
All right, that's as tall as I want it.
I'll till this line again and I'm going to remove it from the blowpipe, I'll hang it up, a little water, and let's go reheat.
Now I'm going to get the top third of that really hot, and I'm going to blow it out.
I'm going to expand it with a steam stick.
I will get it hot as far back as I want it to blow out and I'll use my steam stick in it to create pressure so I can blow it without blowing, and the reason I want to do that is I want to expand that, it's going to be the lip end, okay.
So, now here's my steam stick and see it blow up, so that expanded that.
I need to start that out a little, so now I've got a nice swell to it.
Now we'll begin to open it and I like to use a wooden stick if I can, because it doesn't show glass so much.
Okay, we've got a flare, here we go now, this is going to get real sudden.
So, I'm going to go back, I'm going to reheat, I'm going to spin it and I'm going to (not understandable word).
One quick flash, and I'm going over to crack off now.
You ready?
Now I will smooth that out, put a little extra heat down here, and we'll go into the annealing oven.
That went in nice.
Harvey Littleton was a ceramics instructor at the University of Wisconsin-Madison and they wanted to see if they could come up with a way for one or two people to work with hot glass and to create art with it, and to take it out of the realm of utilitarian, and get it into the realm of art.
I believe, about 1965, may have been earlier, the first class was offered at Madison, Wisconsin.
It was in the Masters of Fine Arts Program.
The furnace that they came up with to melt glass was called a Day Tank.
Those of us that started early used that design of furnace for years and years and then in the factories, in order to cool the glass and take all of the stress out of it they had a unit called a Lehr.
Essentially, it was a metal conveyor belt moving through a heat zone, and it would go from approximately a thousand degrees fahrenheit, and by the time it reached the end it would be down to room temperature.
Of course, that wouldn't work in a small studio, so they came up with an Annealing oven.
Hot glass, once it's melted and formed, must be cooled, slowly, but before it can be slowly cooled, it must be to held at a temperature that's 50 degrees below slumping.
Most glass slumps at around 1050 degrees, but it varies, and there are ways to find out that slumping temperature, but what that Annealing point does, if you hold it at that temperature for up to an hour for thinner pieces, weeks for other pieces - heavy pieces, then it relieves all the strains that are going on inside of that glass, and it allows it then to be cooled slowly and be stress-free so that it doesn't just explode.
Here is one of my finished pieces, you'll notice the metal has all been darkened with heat, the shade is attached, and it's ready to be in somebody's home.
We are at the Crossing Arts Alliance Gallery and Shop in Brainerd, Minnesota, at 711 Laurel Street.
As an artist, I've been making art for a very long time.
I do art fairs and festivals, and I sell my work there, but to have a show set up in a gallery where people can come and visit and talk with me and find out about my art, where my art comes from, where I came from, where my thought process is, understanding the inspiration that drives me; well , without Crossing Arts Alliance in Brainerd, we would have no resource, really, to exhibit our work.
One of the things that the Crossing Arts Alliance does, that Lisa Jordan is so good at, is getting us out in the public eye.
The gallery situation in Brainerd, and the artists, didn't used to be as visible as they are now.
Lisa Jordan has really done a great job of bringing this art, our art, all of the artist's art, out to the community.
Thank you so much for watching.
Join us again on Common Ground.
If you have an idea for Common Ground in north central Minnesota, email us at legacy@lptv.org or call 218-333-3014.
To watch Common Ground online, visit lptv.org and click Local Shows.
To order episodes or segments of Common Ground, call 218-333-3020.
Production funding of Common Ground was made possible, in part, by First National Bank Bemidji, continuing their 2nd century of service to the community.
Member FDIC.
Common Ground is brought to you by the Minnesota Arts and Cultural Heritage Fund with money by the vote of the people.
November 4th, 2008.
If you watch Common Ground online, consider becoming a member or making a donation at lptv.org.
Common Ground is a local public television program presented by Lakeland PBS
This program is made possible by the Minnesota Legacy Amendment and members of Lakeland PBS.